Good News As Many Reach End Of Service Life
The first production A-10 Thunderbolt II was delivered to
Davis-Monthan AFB (AZ) in October 1975. Fifteen years later, the
A-10 was called the most formidable weapon system of its type while
flying combat missions during Operation Desert Storm.
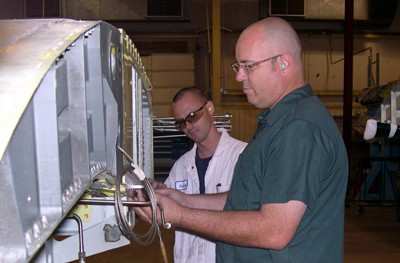
Today, more than 30 years after beginning service, many of the
Air Force’s A-10s are reaching the end of their predicted
8,000-hour service life.
Because there is no replacement for the A-10, aircraft
technicians working on a service-life extension program at the
Aerospace Maintenance and Regeneration Center here are trying to
double the aircraft’s operational lifespan.
Although the aircraft are undergoing countless upgrades, center
specialists are discovering new ways to enhance aircraft repairs
and encountering unexpected problems along the way.
Recently, mechanics discovered a crack in one of the mounts that
connect the center assembly to the outboard wing. The crack was
hardly noticeable to the naked eye.
"There had never been any inspection criteria established
because this was an unpredictable problem," said Sam Smith, A-10
wing production branch chief.
The mount was designed to prevent landing-related stress from
transferring to the wing. It did the job, but not knowing how much
more stress a cracked mount could take was a major concern to the
A-10 team.
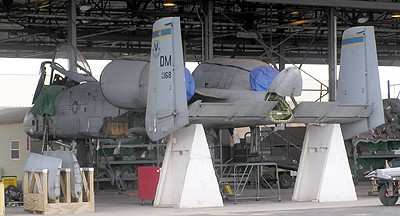
"There is no way to really know if a cracked (mount) could lead
to failure in the aircraft, but our job is to make sure every A-10
is returned to the warfighters in perfect condition," Smith said.
"Every A-10 wing in the inventory is now inspected for cracks in
the (mount). As a result of this unexpected finding a special team
of technicians (here) has developed inspection and repair
procedures to address the problem."
Even with the new technology and procedures used to replace the
wing mounts, each replacement takes two technicians more than 120
hours.
The team creates a template for each mount that meets tolerances
within three-thousandths of an inch -- a degree of error that is
about equal to the diameter of a human hair.
"Once the first crack was discovered, we began the search for
technical guidance on what to do," said Mark Perrodin, a wing
structural mechanic. "There were no technical orders to address the
(mount), and there was no history to show that the problem had been
discovered before. It appeared that the mount was supposed to last
the life of the airframe. But since our goal is to double its
lifespan, we had to find a way to replace (them)."
Technicians found that new mounts were available, but each one
had to be custom-milled to fit each wing set.
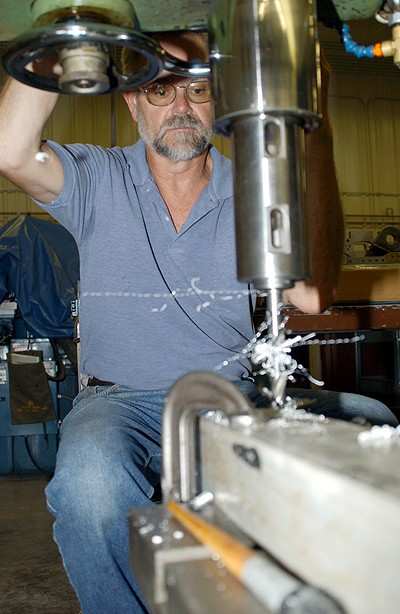
To solve this problem, the team turned to structural mechanic
and expert machinist Tommy Rollins. Starting with a 3-foot-long
block of aluminum, he went to work, inventing a tool that could be
used to customize each wing mount.
"We needed a way to make each new mount match the old one
exactly," Rollins said. "We were able to design and manufacture a
specialized tool to accomplish the task."
Rollins and the mount team not only developed the tool to repair
the wing mounts, they also wrote the procedures for other A-10
teams to follow when repairing these cracks.
At the A-10 systems manager’s request, the tool was
shipped to Ogden Air Logistics Center A-10 Depot at Hill Air Force
Base (UT). It is currently being used to repair similar anomalies
there. Within a week, Rollins was in the machine shop making
another tool for regeneration center workers here.
Once the new mount is milled to exact specifications, mechanics
begin installing it.
First, a template is made to match the exact location and angle
for each of the original 14 mounting holes.
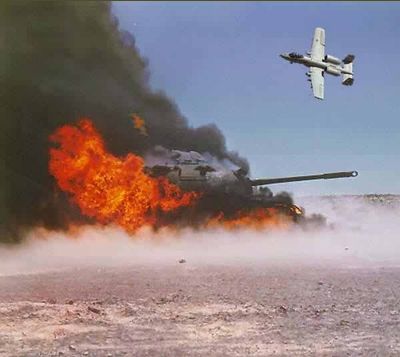
With surgical-like skill, a technician installs the old mount,
marks the location for one hole, replaces the old mount with the
new one and transfers that mark. The procedure must be repeated 24
times to duplicate each individual hole.
Once the new mounts are installed, the wing continues along the
line for work on its hydraulics, electronics, fuel cells, sheet
metal and under-wing hardpoints used to mount weapons.
When completed, each overhauled wing set is rated for up to
8,000 hours of flight time and installed on an A-10 fuselage that
has also undergone a complete refurbishment and upgrades.
Once an aircraft is flight tested, it is ready to return to the
warfighter.
(ANN salutes Tech. Sgt. Brian Davidson,
Aerospace Maintenance and Regeneration Center Public
Affairs)