Wing Separated From The Aircraft During Training Flight
The NTSB has released its probable cause report from an accident involving a Piper PA-28R (Arrow) airplane belonging to Embry Riddle Aeronautical University (ERAU) which occurred April 4, 2018. The commercial pilot candidate and ATP-rated check pilot who were onboard the aircraft were fatally injured in the accident.
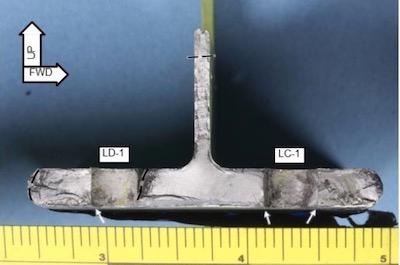
According to the report, an airline transport pilot and a private pilot were performing commercial pilot checkride maneuvers, which included a touch-and-go landing. After the landing and during the climb, the airplane's left wing separated near the wing root and the airplane collided with terrain. The airplane's radar-derived ascent and heading profile following the touch-and-go maneuver was consistent with the airplane maneuvering in a manner that wouldn't reasonably be expected to produce airframe loading that would result in an in-flight structural failure. The airplane was operating under the maximum allowable gross weight and within its center-of-gravity limits at the time of the accident. According to automatic-dependent surveillance broadcast data, the airplane's radar target was last recorded at an altitude of 900 ft mean sea level (msl) and a groundspeed of 80 knots. Witnesses within 1/4 mile of the accident site reported that the airplane climbed "normally" on a westerly heading when they
saw the wing separate from the fuselage.
Metallurgical examination of the accident airplane's left-wing main spar lower cap found that it exhibited fracture features consistent with fatigue through more than 90% of the cross-section, reducing its residual strength capabilities almost completely. The examination identified three fatigue cracks in the left-wing main spar lower cap (see figure 1). One fatigue crack initiated near the lower forward corner of the outboard forward wing attachment bolt hole (designated as bolt hole LC-1) and propagated forward to the forward edge of the cap. A second fatigue crack initiated near the lower aft corner of bolt hole LC-1 and propagated aft toward the lower aft wing attachment bolt hole (designated as bolt hole LD-1) and up the cap web almost to the edges. A third fatigue crack initiated near the lower aft corner of bolt hole LD-1 and propagated aft almost to the aft edge of the cap. Fatigue cracks also originated in the forward and aft doublers from both sides of the bolt holes.
A small fatigue crack was also identified in the accident airplane's right-wing main spar lower cap; however, that crack had not progressed to the point of failure. Examination of the left-wing main spar of another Piper PA-28R-201 owned and operated by the same operator as the accident airplane; manufactured in the same year with a serial number two previous to the accident airplane; and with similar hours, cycles, and operational exposure found a similar fatigue crack that initiated near the lower forward corner of hole LC-1.
The accident airplane was manufactured about 10 years before the accident and had been used solely for flight instructor and commercial pilot training by the flight school operator. The airplane had accumulated 7,690.6 hours and 33,276 landing cycles before the accident flight, which equates to 4.33 landing cycles per hour of flight time. According to operator personnel, the commercial flight lesson times averaged 1.4 to 1.8 hours; most of that time the airplane was being operated in the airport traffic pattern, performing takeoffs, landings, and power-off 180º maneuvers. While in the airport traffic pattern, the airplane operated between 1,000 ft agl and ground level. On longer flights, necessitating the need to operate in the practice area, maneuvering typically took place between 2,500 and 3,000 ft msl before returning to the airport.
A review of the operator's airframe discrepancy log for the life of the airplane and flight crew safety reporting system for the 24 months preceding the accident found some reported flap extension overspeed, gear extension overspeed, and hard landing events. In each case, the events resulted in airframe examinations during which no defects were noted by maintenance personnel. Interviews with flight instructors did not yield any safety of flight issues or critical airframe or loading exceedances caused by pilot operation that would be expected to precipitate cracking.
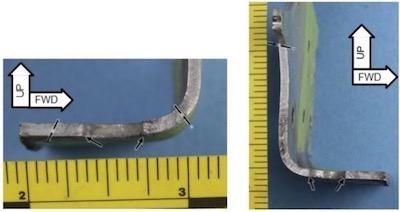
The operator's maintenance program alternated between 50-hour and annual inspections that included airframe manufacturer-recommended inspection items. The annual inspection detailed in the airframe manufacturer's maintenance manual includes a specific line item to inspect the wing attachment bolts and brackets that was included in the operator's inspection. There were no specific instructions from the airplane manufacturer or additional steps from the operator for a detailed inspection of the wing main spar lower caps in the area where the fracture occurred. A review of the maintenance logbook for the entire life of the airplane found no indications of airplane damage, major repairs, or significant nonstandard maintenance concerning the wing structure.
About 31 years before this flight training accident, in response to a pipeline patrol accident in which the left wing separated from a PA-28-181 airplane, the airframe manufacturer issued Service Bulletin (SB) 886 recommending a visual and dye penetrant inspection of the wing main spar on certain PA-28, PA-28R, and PA-32 model airplanes. The initial and recurrent inspection intervals recommended by the SB were calculated based on an accounting of the affected airplanes' lifetime usage, which the SB categorized into four usage classes: normal, severe, extreme, and unknown. Based on the SB criteria for the normal usage class, which included normal flight training operations, the accident airplane was not due for an initial inspection for another 23,000 flight hours (the SB recommended an initial inspection of the wing main spar at 30,600 hours).
Considering the absence of anomalies in materials or construction of the examined wing spars from N106ER and N104ER, the disparity between the failure time of the accident wing spar and the inspection threshold time in the SB likely derives from the differences between normal usage (as analyzed after the pipeline patrol accident that prompted the SB) and the actual flight training usage experienced by the accident airplane. The Piper PA-28R-201 and other similar airplanes were type certificated under Part 3 of the Civil Air Regulations, which only required that design details avoid stress concentrations; thus, this airplane model and others similar to it was not subject to the more robust fatigue analysis requirements under Title 14 Code of Federal Regulations (CFR) Part 23. In 2005, the FAA published Advisory Circular (AC) 23-13A with information and guidance for performing fatigue, fail-safe, and damage tolerance evaluations of metallic airplane structures developed under Part 23 regulations.
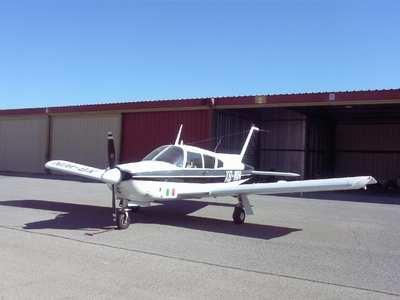
AC 23-13A provides flight and ground load information for various types of flight operations. AC 23-13A includes detailed information on the flight gust and maneuver loads, load factors for taxi movements, and landing sink rate data that can be used to determine flight and ground loads for the various types of operations for single-engine airplanes. These flight and ground loads drive the aging and fatigue of metallic airplane structures. The NTSB's investigation referenced this information to evaluate the flight and ground loads that the accident airplane was likely exposed to over its operational life in the flight training environment. This evaluation found that the maneuver loads experienced by the accident airplane were likely similar to the maneuver loads for basic instruction published in AC 23-13A, which are slightly higher than for personal use. The gust loads in the accident airplane flight training environment could also be higher than in the personal use environment (in the personal use
environment airplanes are typically operated at higher altitudes, and gust loads are generally more severe and frequent at lower altitudes for any given airspeed). However, the gust loads for basic instruction are presented as identical to personal use in AC 23-13A. Loads associated with taxi movements for the accident airplane were likely similar to those of other operations other than agricultural application as shown in AC 23-13A. Landing impact loads for the accident airplane were likely higher and more frequent than other types of operations. Sink rates for basic instruction use as published in AC 23-13A are higher than that of other uses including the pipeline survey use and normal use analyzed for SB 886, and higher sink rates correspond to higher landing impact loads.
The NTSB concludes that, due to flight training maneuvers, significant operation at low altitudes, and frequent landing cycles, the accident airplane (and its sister airplane in the operator's fleet) likely experienced landing, gust, and maneuver loads that were more severe than expected for training aircraft when SB 886 was developed. Therefore, the low-altitude flight training and frequent landing environment likely resulted in the accident airplane accumulating damaging stress cycles at a faster rate than a personal use airplane.
After the accident, 16 airplanes from 4 flight schools (including ERAU) were examined using eddy-current inspection of the outboard attachment holes. Times in service ranged from 2,777.5 to 10,301.5 hours, and estimated landing cycles ranged from 8,841 to 39,000 cycles. Among the inspected airplanes, a crack was found in one wing of ERAU airplane N104ER, which had a time in service of 7,660.7 hours and 33,288 landing cycles. No additional cracks were detected in the remaining airplanes, including four airplanes with higher estimated landing cycles. However, due to the limited sample size and the expected variability in fatigue crack initiation times, the absence of detected cracks in airplanes with more cycles and/or hours than N106ER and 104ER does not eliminate the risk of fatigue cracking due to loads associated with a more severe training environment.
The location of the fatigue cracking observed on the accident airplane's left-wing main spar lower cap would have prevented visible detection from the interior or exterior of the airplane. Evidence of the presence of a crack would only have been visible after cracking had begun in the doubler and grown past the bolt head to a significant length. The only reliable method to detect the fatigue cracking in the wing main spar, as installed, would have been a nondestructive inspection procedure, such as a high frequency eddy current bolt hole inspection. The FAA issued a notice of proposed rulemaking 8 months after the accident proposing to require such an inspection for all Piper PA-28 series airplanes, except the PA-28-201T and PA-28-236 model airplanes; all Piper PA-28R model airplanes; and all Piper PA-32-260 and PA-32-300 model airplanes. In the NTSB's February 15, 2019, comments to the FAA, we expressed our support of the proposed AD's inspection requirements but urged the FAA to reexamine the
proposed AD's applicability to certain airplanes based on airplane usage. As of the date of this report, the FAA has not published an AD for inspection of the accident airplane type and other similar types, especially those operated in the flight training environment.
The NTSB determined the probable causes of this accident to be extensive fatigue cracking in the left-wing main spar lower cap and doublers, which resulted in the in-flight separation of the left wing. The fatigue cracks initiated and grew to a critical size due to flight and ground loads associated with flight-training involving flight-training maneuvers, significant operation at low altitudes and frequent landing cycles. Previously established inspection criteria were insufficient to detect the fatigue crack before it grew to a critical size.
(Images provided with NTSB probable cause report. PA-28R image from file. Not accident aircraft)