Development Funded By The EU's Clean Sky 2 Research Project
As the geared turbofans (GTFs) of the first generation are busy clocking up mileage in revenue service, MTU Aero Engines engineers already have their hands full working on the second generation: Under the European Union’s Clean Sky 2 research project, Germany’s leading engine manufacturer continues to enhance the fuel-efficient, low-emission, low-noise propulsion system, developing new technologies for two of its modules, the low-pressure turbine and high-pressure compressor. Two demonstrators are being built to validate the new technologies.
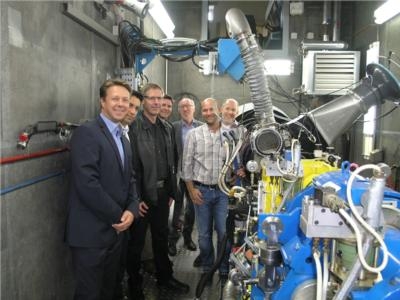
“Under Clean Sky 2, we are paying special attention to the interactions of the components sitting on the low-pressure and high-pressure shafts,” explains Dr. Stefan Weber, Senior Vice President Technology and Engineering Advanced Programs at MTU Aero Engines. Investigations into the low-pressure turbine will also take the inlet and exit case designs into consideration, and the optimization of the high-pressure compressor will also involve improvements to the low-pressure compressor and inter-turbine case. The efforts aim to further enhance the aerodynamics and to develop new, lighter-weight and more temperature-resistant materials. Among the materials that hold the greatest promise for low-pressure turbine applications are among others ceramic matrix composites, or CMCs for short.
An MTR390 engine will be used for the validation of the new low-pressure turbine technologies. This propulsion system was made available to MTU by the German Armed Forces’ Technical Center WTD61; it had already been in service on a Tiger helicopter. “We received the engine in October, inspected it and, jointly with WTD 61 representatives, conducted a test run to verify the performance parameters,” reports Dr. Gerhard Kahl, Chief Engineer, Technology Demonstrators and Rigs at MTU. The test run demonstrated that the temperatures in the turbine get as high as is required for the planned material tests.
"The engine is now being converted into a demonstrator, for it will be necessary to design and build a complete new power turbine and assemble it to the core engine for the integration of the newly developed materials. “Plans are to get the demonstrator up and running and tested by 2020. We expect the evaluation of the results to be concluded in 2021.“ An analysis of the behavior of the materials in an engine environment will then provide proof of the maturity of the technology,” says Kahl.
To further enhance the compression system, the ICD rig is being built and tested at the German Aerospace Center (Deutsches Zentrum für Luft- und Raumfahrt (DLR)) in Cologne. ICD stands for the inter-compressor duct located between the low-pressure and high-pressure compressors. “Our goal is to precisely fine-tune the low-pressure compressor, ICD and high-pressure compressor to leverage new potential for even more fuel-thrifty engines,” Weber said.
An important step in this direction is the systematic mapping of the flow conditions in short, steep ICDs. To this aim, an entirely new wind tunnel rig was built at DLR in Cologne, MTU’s Center of Competence (CoC) for propulsion systems. “Over the course of next year, three different ICD configurations will be tested,” announces Kahl. Based on the ICD rig test results obtained, a two-shaft rig will be designed in 2019 and built one year later. After that, the low-pressure and high-pressure compressors and the ICD will be tested as one entity. “The technologies validated could already go into the next generation of geared turbofan engines starting in 2025,” reports Weber.
Launched in 2014, the Clean Sky 2 technology program is part of the EU’s Horizon 2020 Framework Program for Research and Innovation and is slated to run through 2024. Its primary aim is to make aviation even more environmentally friendly and efficient.
(Source: MTU news release. Image provided)