Develops CAD Design Tool For Automated Generation Of Bionic Components And Subsequent Output To Additive Manufacturing
About a year after the launch of the EU’s ground-breaking Bionic Aircraft project, CENIT reports concrete initial results. These include software for automated recognition of topologically optimized structures, an associated catalogue of parameterized bionic characteristics in CAD, and a tool for direct generation of file formats for 3D printing.
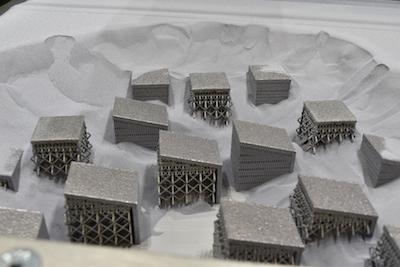
Since September 2016, IT and software provider CENIT has collaborated with nine international industry and research partners in the EU’s “Bionic Aircraft” project, developing new methods and concepts for additive aircraft design and manufacturing. The overarching goal of this research work is to achieve significant advances in resource efficiency. A decisive contribution is expected to come from the development and implementation of technologies for additive layer manufacturing (ALM) / 3D printing) and bionic design in all phases of the aircraft lifecycle.
The primary aim of CENIT’s tasks is to radically simplify the design process for lightweight bionic structures. Core aspects of CENIT’s approach include an automated design methodology and a tool for direct generation of specific file formats for 3D printing. The project partners have set themselves the goals of slashing the time needed for end-to-end development of bionic components by about 40% and significantly increasing the weight-saving potential of ALM structures.
An ambitious endeavor that is now producing the first results: To create bionically optimized components, CENIT is developing a CATIA-based CAD catalogue of parametrically defined bionic features. “This provides an automated toolbox to support the cost- and time-intensive manual interpretation and design of topologically optimized components in CAD”, says Jochen Michael, Senior Consultant at CENIT, in explaining the objective. “The parametrization of features also lets the designers adjust geometries more easily. That gives us an additional efficiency and quality boost during the design process”.
By the end of the Bionic Aircraft project in August 2019, CENIT expects to have developed a CAD catalogue containing about 10 to 15 bionic features. “The declared goal of the project is to show how such a catalogue can be implemented in methodological and practical terms. That places the focus on fundamental research. It has to provide a basis for defining how bionic features can be harnessed to guide topological optimization, and what algorithms are best suited to component recognition and allocation of features”, explains CENIT’s Jochen Michael. With this research, the project partners are breaking new ground – to date, no CAD program contains bionically optimized features.
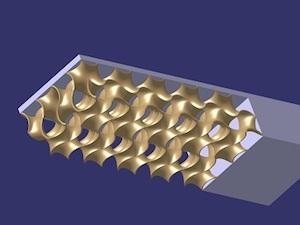
For expertise on the nature, suitability and functionality of the bionic features which CENIT is integrating into CAD, the project is relying on experts from the Fraunhofer Institute for Additive Production Technologies, IAPT. Based on analyses on qualitative characteristics, uses and benefits of topology-based components, they develop the respective bionically optimized features. The aim is to improve the typical behavior of components in everyday use, and to make them as lightweight and stable as possible. An example of how even minor adjustments can achieve a significant effect: The risk of component failure can be significantly reduced if components subject to tension loads are designed with fillets which replicate models found in nature. Thus, such a feature will be included in the CAD catalogue as a parametric model.
After programming the first bionic features in CAD, CENIT will take on the next project milestone: Feature recognition. This is a software tool that analyzes a topologically optimized component and allocates it – if possible, fully automatically – to a functionally equivalent bionic feature contained in the CAD catalogue. This capability makes feature recognition an important element in the design of bionic ALM components.
In addition to bionic design, CENIT’s work package also involves print preparation (pre-processing) aspects. Here the main focus is on CAD-based generation of the support structures needed for 3D printing and optimum alignment/orientation of components prior to printing.
To develop the support structures, CENIT relied on the results achieved by its research partner Fraunhofer IAPT. The institute conducted systematic studies on criteria such as tensile strength, powder consumption as well as removability of support structures and their influence on component surfaces. It also developed approaches to designing new types of support structure, e.g. graded lattice scaffolds or gyroids.
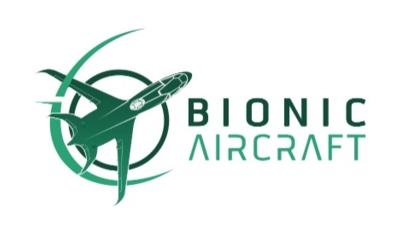
Based on the wide range of parameters needed to determine the orientation of a component for additive layer manufacturing, CENIT’s experts worked with CATIA to also develop functionalities for optimal, automated alignment of components, including the required support structures. CENIT’s project work is now focused on supplying the production process not only with geometry data but also with geometry attributes (e.g. external contour, surface quality, etc.) as well as defining printing methodologies. In collaboration with Aconity GmbH, CENIT is currently developing a direct CATIA interface.
The ten partners of the Consortium will present these and other outputs to the EU Commission on the occasion of the midterm review of the Bionic Aircraft project in April 2018.
(Images provided with CENIT news release)