Special Military Team Searches For Aircraft Cracks
All combat aircraft go through extreme stresses when completing
their missions. Those stresses can cause metal fatigue -- tiny
cracks in the joints and welds of the frame or invisible fractures
in the metal.
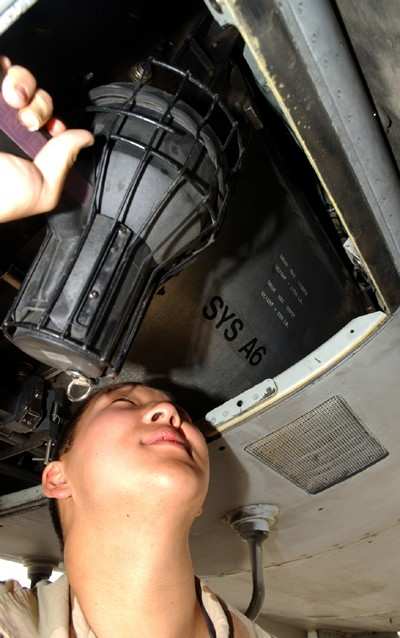
The sooner these invisible cracks are found, the safer the
aircraft will be.
Finding those cracks in a deployed environment, where every
aircraft is critical and ensuring they are fully operational is of
premium importance, is the mission for three airmen at the Bagram
Airbase in Afghanistan. The nondestructive inspection team is part
of the fabrication flight and uses various techniques to find
cracks in the metal on aircraft here, said Senior Airman Ryan
Michalec, of the 354th Expeditionary Aircraft Maintenance
Squadron.
"We use different scientific methods to find those cracks that
can’t be seen by the unaided eye, as well as those which
can," he said.
The tools the team uses are fairly similar to those they use at
home; however, the tools here are portable.
"We had an X-ray machine that we couldn’t bring because of
its size," said Staff Sgt. Brooke Wilke, a team member. "The
portable equipment takes a little more time, on occasion. For
example, inspecting the A-10 (Thunderbolt II) main landing gear
wheel bolts (takes) a little more time with the magnetic particle
unit we have here instead of the equipment we would use at
home."
This gives team members experience with many different pieces of
equipment.
"I’ve gotten a lot of training [that] I wouldn’t
have at home," said team member Airman 1st Class Kevin Louie. "I
have gotten the chance to work with other services and on other air
frames, [too]."
The goal for the team is to avert catastrophic problems without
tearing up the airplane to find them.
"It takes us a few minutes to find cracks; it may take some time
for a maintenance crew to get to and repair," said Sergeant
Wilke.
The team uses many different processes to find metal fatigue.
For instance, with one technique, the technician places a long,
thin probe on the aircraft part.
"The probe creates a magnetic current in the metal. We can read
changes in that current [called an eddy current] to determine where
the cracks are," Airman Michalec said.
He explained the process by using the analogy of throwing a
stone into still water. The stone causes eddies in the water, and
any obstruction in the water will cause a disruption in the smooth
progression of the eddies.
Another technique uses ultrasonic sound waves to locate
cracks.
"If there’s a crack in a part, you get a signal loss or a
reduced signal from the ultrasound, if you use this technique,"
Airman Louie said.
Not everything is as technically complex. One of the techniques
used most often by the team is oil analysis, where the technician
checks how much worn metal is in the engine oil by burning a sample
in a special machine.
"We can determine if an engine is starting to go bad by
examining the oil," Sergeant Wilke said. "Sometimes you can go a
long time before getting a ‘hit’ indicating a
deteriorating engine, and then you might have one or two in a few
weeks."
So far, in the four months the team has been deployed to
Afghanistan, it has had two "hits" on A-10 engines and one on an
MH-47 helicopter transmission, Sergeant Wilke said.

"The level of flying hours here (generates) a lot more activity
on the aircraft [because] each plane flies regularly," she said.
"That makes a lot more oil samples for us to check."
Keeping the aircraft safe is extremely important to the
team.
"I want to do anything I can to prevent a show-stopper --
something that will keep the aircraft from doing its mission,"
Airman Michalec said. "If no one was checking, we might have more
mishaps. This job is really important. It makes me feel good to
know I have such a vast impact in keeping the plane
operational."
The focus on nondestructive inspections sets the team apart from
other services as well.
"In most of the other services, this job is in addition to the
maintainers’ normal job," Airman Michalec said. "We are
dedicated to this mission and are specifically trained to do
it."
(ANN salutes Master Sgt. Andrew Gates, 455th Expeditionary
Operations Group Public Affairs, USAF)