Produced Replacement Blade Inspection Method Vents (Bim Vents) For The Aircraft’s Main Rotor Blades
Fleet Readiness Center East is celebrating an achievement, and likely first, in using 3D printing and polymers as a supply solution to repair components for the H-53E.
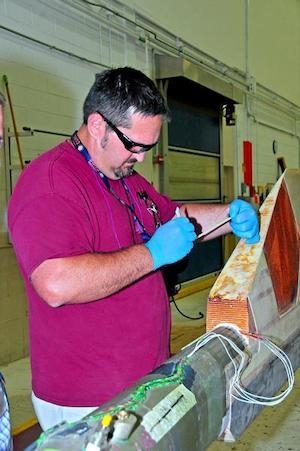
Research and Engineering Group engineers used a polymer additive manufacturing process — fused deposition modeling — to produce replacement blade inspection method vents (BIM vents) for the aircraft’s main rotor blades. “I believe this is the first time a polymer AM process has been used to build a flight critical repair component in (Naval Air Systems Command),” said Douglas Greenwood, AM Lead for the Advanced Technology Integrated Product Team. “We don't usually, if ever, see ‘polymer AM’ and ‘flight critical’ in the same sentence.”
According to Joshua Peedin, senior engineer for H-53 Rotor Systems, artisans in Blade Shop 94304 identified integral damage in the parts during the repair process in 2016. It was a discovery of cracks in the foam beneath the root fairing that pointed to the damage in the vents.
The BIM vents work as part of the indication system to alert pilots to pressure loss in the blades. The BIM vents are critical application items, which means they have a critical function for a major component; not critical in terms of safety of flight.
Peedin said that unavailable parts led him in the direction of the solution. I contacted our logisticians and (the OEM) to see if we could buy any replacements,” he said. “Neither had any available, so I checked the technical drawings to see if we could manufacture our own replacements.”
He said making composite molded replacements were considered, but the composite material was too rigid to meet the required specifications.
Peedin said Materials Engineers Rob Thompson and Andrea Boxell, from the Polymers and Composites Branch, pointed out FRC East’s capability of 3D printing the part using a material that is chemically similar to the original material — a high-performance, thermoplastic polyetherimide. He also got the help of FRC East Digital Data Center members Justin Reynolds and Todd Spurgeon, AM subject matter experts, to redesign the BIM vents to ensure design compatibility with FRC East’s 3D printers. “We had many meetings throughout the process to ensure everyone was in agreement to move forward,” said Peedin.
The prototype repair parts were tested under pressure and heat to ensure the repair could withstand in-service conditions and future blade repairs. The local engineers developed, documented, reviewed and approved the repair procedure through AIR-4.3 Air Vehicle Engineering. The repair was first successfully demonstrated on a scrap main rotor blade asset. The most recent BIM vent repair was the second performed on a production main rotor blade asset using the AM parts.
Greenwood said the accomplishment is also noteworthy, as it demonstrates the flexibility of AM processes. He said FRC East primarily uses the AM printers to make sheet metal form blocks, prototype parts, visual aids, support equipment and many other kinds of parts to support FRC East production. "All of those parts are built using materials different from the BIM vent parts and none of them are intended for use in flight,” said Greenwood. “Nevertheless, we are using the same printers with a different material to make the BIM vent repair parts.”
Greenwood added, the BIM vent parts mark a new milestone for FRC East. “This is an even bigger achievement for FRC East,” he said. “Using our printers to make polymer AM repair parts on H-53E main rotor blades that will enter the supply system and be used by the fleet.”
The accomplishment offers benefits in the way of cost avoidance, production and aircraft readiness. eedin said the estimated cost to make the type of repair to blades through fused disposition modeling is about $15,000 per blade. The pre-existing alternative to the fused deposition modeling repair was to pay the OEM to overhaul the main rotor blade for about $210,000 per blade; a $195,000 savings per blade.
Peedin said, FRC East is now able to keep a steady flow of main rotor blade repair work in the blade shop. “This will lead to a reduction of backordered repairs and ultimately contribute to improvements in the H-53 readiness posture,” he said.
(Image provided with NAVAIR news release. Aircraft Mechanical Parts Repairer Todd Bridgers applies a gel viscosity instant adhesive to a blade inspection method (BIM) vent.)