Former Marine Helo Converted Into Research Platform
NASA researchers are set to drop a 45-foot-long helicopter fuselage from a height of about 30 feet for the second time in a year – all in the name of safety.
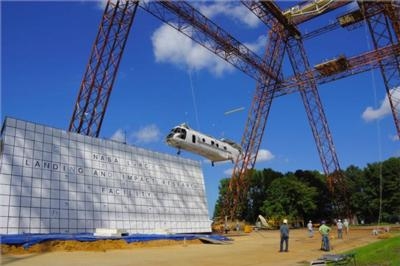
NASA is collaborating with the U.S. Navy, U.S. Army, FAA, the German Aerospace Center (DLR), and the Australian Cooperative Research Center for Advanced Composite Structures on the Transport Rotorcraft Airframe Crash Test Bed full-scale crash test at Langley's Landing and Impact Research Facility.
"The big difference in this year's experiment is that we are testing three energy absorbing composite subfloor concepts that should help some of the dummy occupants sustain fewer injuries than they did in the first test last August," said lead test engineer Martin Annett. "We have also made other improvements based on things we learned."
The team has instrumented a former Marine helicopter airframe with crash test dummies, cameras and accelerometers. Almost 40 cameras inside and outside the helicopter will record how 13 data-recording crash test dummies and two manikins react before, during and after impact.
Some of those cameras will be trained on the side of the helicopter where technicians have painted black polka dots over a white background -- a photographic technique called full field photogrammetry. "High-speed cameras filming at 500 images per second track each dot, so after the drop we can plot and see exactly how the fuselage buckled, bent, cracked or collapsed under crash loads," said test engineer Justin Littell.
During the test, onboard computers will record more than 350 channels of data as the helicopter is swung by cables, like a pendulum, into a bed of soil. Just before impact, pyrotechnic devices release the suspension cables from the helicopter to allow free flight. The helicopter will hit the ground at about 30 miles an hour. The impact condition represents a severe but survivable condition under both civilian and military requirements.
"The crash won't look all that visually exciting," said Annett. "Unlike in the movies there's no huge fireball or spectacular special effects, but the occupants certainly get a jolt. According to the data some of the dummies would have sustained serious if not fatal injuries in last year's crash test."
Both tests are part of the Rotary Wing Project in the Fundamental Aeronautics Program of NASA's Aeronautics Research Mission Directorate.
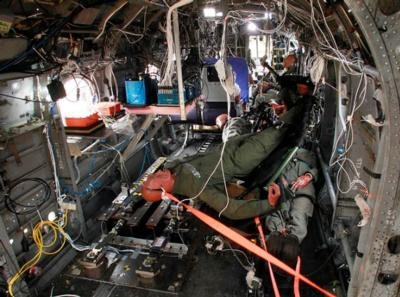
"We are looking for ways to make helicopters safer," said Rotary Wing Project Manager Susan Gorton. "The ultimate goal of NASA rotary wing research is to help make helicopters and other vertical take off and landing vehicles more serviceable -- able to carry more passengers and cargo -- quicker, quieter, safer and greener. Improved designs might allow helicopters to be used more extensively in the airspace system."
For this test NASA supplied six crash test dummies, built two composite subfloor concepts and installed four emergency locator transmitters that researchers are evaluating. The Navy provided the CH-46 Sea Knight helicopter fuselage, seats, crash test dummies and other experiments. The US Army Aeromedical Research Lab (USAARL) contributed a litter experiment and the Army CH-47 program office (PEO CARGO) provided a crash resistant troop seat.
The Federal Aviation Administration provided a side-facing specialized crash test dummy and part of the data acquisition system. Cobham Mission Systems also contributed an active restraint system for the cockpit. The German Aerospace Research Center (DLR) and the Australian Cooperative Research Center for Advanced Composite Structures supplied a third composite subfloor technology. Other industry participants have also contributed experiments.
NASA will use the results of both tests in efforts to improve rotorcraft performance and efficiency, in part by assessing the reliability of lightweight composite materials. Researchers also want to increase industry knowledge and create more complete computer models that can be used to design safer helicopters.
(Images provided by NASA)