Leverages VABS Software for More Realistic Simulation Of Helicopter Rotor Blades
Carleton University in Ottawa, Canada is participating in a new program to study helicopter rotor design. The university recently launched an Academic Partner Program (APP), and is using VABS simulation software developed by AnalySwift for simulating new helicopter rotor blades. The work is part of the Rotorcraft Laboratory at Carleton University, a research group working on new comprehensive software for helicopters in order to study various tasks such as aerodynamics, structural dynamics, flight mechanics, and control. Supervised by Dr. Fred Nitzsche, Professor in the Mechanical and Aerospace Department, over the past 20 years, the Rotorcraft Laboratory collaborates with several European universities to accomplish these tasks.
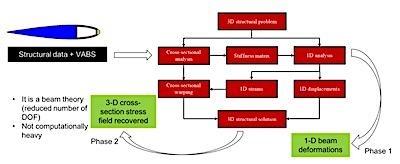
The Academic Partner Program (APP) offers participating universities no-cost licenses of engineering software programs VABS and SwiftComp so students, researchers, and faculty can leverage the tools in their academic research. It also affords students an additional avenue to highlight their research as AnalySwift periodically spotlights papers, theses, and articles involving the codes. A robust community of users helps answer questions through the online cdmHUB (composite design & manufacturing HUB) platform.
The VABS program is a general-purpose cross-sectional analysis tool for computing beam properties and recovering 3D stresses and strains of slender composite structures. It is a powerful tool for rigorously modeling composite helicopter and wind turbine rotor blades, as well as other slender structures, such as propellers, landing gear, and high-aspect ratio wings.
“We are excited by the work being done by Carleton University and are pleased they have selected VABS as part of their composite helicopter rotor blade simulation workflow,” said Allan Wood, president & CEO of AnalySwift. “As a versatile cross sectional analysis tool, VABS saves orders of magnitude in computing time without a loss of accuracy so engineers can consider more design options and arrive at the best solution more quickly. This allows users to accelerate project completion while reducing costs.”
“Many helicopter and wind turbine blades are made of composite materials and have relatively complex geometry,” said Dr. Ali Siami, postdoctoral fellow in the Mechanical and Aerospace Department of Carleton University. “In order to model them correctly, the structural properties of these blades should be extracted thoroughly. VABS, which calculates the structural properties of blades, will be used in this project to accomplish this. The results of this project will be used to design rotorcraft with more realistic models that are provided in the new developed software. The results can also be extended to wind turbines.”
“The VABS program is a uniquely powerful tool for modeling composite blades, high aspect ratio wings, and other slender structures, commonly called beams,” said Dr. Wenbin Yu, CTO of AnalySwift. “VABS reduces analysis time from hours to seconds by quickly and easily achieving the accuracy of detailed 3D finite element analysis (FEA) with the efficiency of simple engineering models. With VABS, engineers can calculate the most accurate, complete set of sectional properties such as torsional stiffness, shear stiffness, shear center for composite beams made with arbitrary cross-section and arbitrary material. It can also predict accurate detailed stress distribution for composite beams, which are usually not possible with 3D finite element analysis (FEA) for realistic composite structures.”
(Infographic provided with AnalySwift news release)